Nori bricks, which were first fired in the Lancashire town of Accrington in 1887, quickly became legendary as the hardest brick ever produced. Their strength, derived from the chemical properties of the local clay, enabled megastructures to rise up around the world, including the Blackpool Tower in 1894 and the Empire State Building in New York in 1930. Their name is said to be a cock-up from when they meant to write “iron” on the works’ chimney.
This year a different, though equally pioneering, construction material is set to bring attention to the town, which is 20 miles north of Manchester and whose most recent claim to fame is being trash-talked in a 1989 advert for milk. On Charter Street, on a patch of disused land owned by the council, there are plans to build 46 net-zero-carbon homes, ranging from single-bedroom apartments to four-bed houses, all occupied by low-income families or military veterans. The homes will be made not from Nori bricks, but from 3D-extruded concrete. When the development is complete, potentially in late 2023, it will be the largest printed building complex in Europe.
“My grandad actually used to work at the brick factory,” says Scott Moon, born-and-raised in Accrington, whose company, Building for Humanity, is behind the Charter Street project. “When I was young he used to take me in there at night and I used to ride on the back of the forklift. So, bless him, if he could see us now, about to start concrete-printing houses in Accrington…”
You remember 3D printing – also known as additive manufacturing – right? You probably read an article around 2012 that predicted how every home would soon have a 3D printer that we would use for all manner of ingenious tasks. OK, well that didn’t happen. “Nobody’s going to be making bits for their washing machine when it breaks,” says Richard Hague, professor of additive manufacturing at the University of Nottingham. “People making handles for their saucepans when they drop off? No one’s going to do that and you’d be mad if you did. You can just order stuff from Amazon quicker and get it delivered the next day.”
But while home usage of 3D printers has not taken off, stealthily the technology has been inveigling its way into our lives in other ways. Almost all – 99% plus – custom hearing aids are now 3D printed in acrylic resin, and have been for years. Additive manufacturing is widely used in dentistry: teeth aligners, which are increasingly taking the place of traditional wire braces, would be almost impossible without 3D printing. Adidas and Nike use the technology in their shoes. There are 3D-printed parts on all new aircraft and in a growing number of cars.
“What happened 10 years ago, when there was this massive hype, was there was so much nonsense being written: ‘You’ll print anything with these machines! It’ll take over the world!’” says Hague. “But it’s now becoming a really mature technology, it’s not an emerging technology really any more. It’s widely implemented by the likes of Rolls-Royce and General Electric, and we work with AstraZeneca, GSK., a whole bunch of different people. Printing things at home was never going to happen, but i t’s developed into a multibillion-dollar industry.”
That’s no exaggeration: the 3D-printing market is forecast by Hubs, a marketplace for manufacturing services, to almost triple in size by 2026, with a value of $44.5bn. Construction is one of the growth areas. In 2018, a French family and their three children became the first family to live in a 3D-printed home. The four-bedroom bungalow in Nantes took 54 hours to print and cost £176,000. More ambitious structures have followed in the Netherlands, the US and Dubai. The Accrington project has been made possible by recent developments in load-bearing printable concrete that performs well, but is also cost-effective.
“In very, very basic terms, you have a rig that sits onsite, over where the house is going to be,” explains Dr Marchant van den Heever, a structural engineer who works for Dublin-based Harcourt Technologies (HTL), the construction partner of Building for Humanity on the Charter Street project. “And you have a material-delivery system. So you mix up concrete, which you feed into the printhead. And essentially this printhead is like a gigantic cake-icing machine that extrudes concrete, one of the most robust materials in the world.
If you imagine a book, each page in the book is a layer of concrete,” van den Heever adds, “and these consecutive layers stack on top of one another and that forms your superstructure.”
The cake analogy is a helpful one. Early 3D-construction projects typically have a ribbed, Michelin-Man exterior, like the piped finish of a rushed showstopper challenge on Bake Off. But the sophistication of the finish is improving fast and slick 3D-printed buildings often now appear in stories for the likes of design website Dezeen and Architectural Digest. But what really excites companies such as Building for Humanity and HTL are the potential savings and efficiencies the new technology offers. Charter Street has a projected budget of £6m, an estimated 25% cost reduction against comparable construction. It will be made with sustainable, often recycled materials in what they hope will be half the site time – 101 working days, instead of more than 12 months.
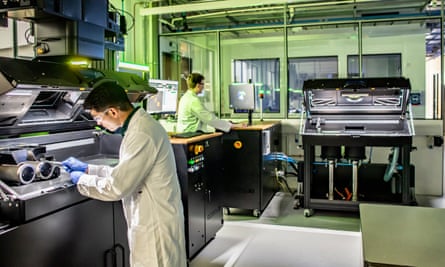
“To be cost-competitive from the get-go is quite unheard of for an emerging technology,” says Justin Kinsella, an architect who founded Harcourt 20 years ago and who is making his first foray into 3D-printed buildings. “We’re just excited to actually have people come on site, slam the door, the wall doesn’t wobble. Kick the wall, that doesn’t move. The roof is there. Switch the lights on, that’s proof and people will then, I think, be astounded by it.”
First described in sci-fi writing in the 1950s, 3D printing became a very basic reality in the 1980s. The core principles remain the same today: an object is created layer by layer – hence additive – from the ground up. (Imagine sedimentary rock forming, just really, really fast.) This might be done by physically extruding a material, as in the construction project in Accrington, or it could be computer-guided laser beams that make layers, which can be as thin as a human hair, by melting powders of metal, plastic or other materials. One of the great, immediate advantages of additive manufacturing is that you only print what you need. This contrasts with machining a lump of metal, for example, where you might carve away most of it, which is then wasted or needs to be recycled.
In the early years, though, 3D printing was expensive, slow and prone to gaffes. Only recently has the technology developed to overcome some of these flaws. Also, there has been a stark realisation that 3D printing is not going to be a magic bullet. “I might come across like an enthusiastic child and I am really enthusiastic,” says Hague. “But I’m super-realistic about what can and can’t be done. And so you’re not going to be doing everything with additive.”
One of the areas of excitement a decade ago was the idea of 3D printing food. In this vision of the future, we would come down to breakfast to a freshly printed croissant or pop some dough in the machine, tap a few buttons and come back to “homemade” ravioli. The new products would also address one of the great challenges of our age – that one-third of the food produced in the world, about 1.3bn tonnes, is wasted.
It was this statistic that brought 26-year-old Elzelinde van Doleweerd, a graduate in industrial design from the Eindhoven University of Technology in the Netherlands, into the field. She began experimenting with bread, fruit and vegetables, the most commonly spoiled food in northern Europe, to see if dehydrating them and changing them into beautiful shapes could give them a second life. This led to a six-month placement in 2021 in the test kitchen at the Copenhagen restaurant Alchemist, which is currently ranked 18th on the world’s 50 best list.
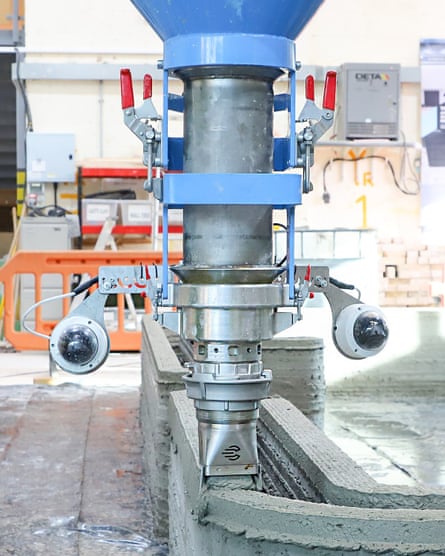
At the end of her stint at Alchemist, van Doleweerd had refined a beetroot and carrot “tartelette” that was served on 3D-printed petals made from chitosan, a sugar derived from the outer skin of shellfish, and garnished with edible flowers. It looks stunning – “It’s a good vibe!” confirms van Doleweerd – but has yet to make it on to the menu at Alchemist because of the difficulties of producing it under pressure at every service.
For van Doleweerd, who now works in the food lab at Restaurant De Nieuwe Winkel in the Netherlands, which has been rated the world’s best plant-based restaurant, it is hard to imagine 3D-printed food entering the mainstream soon. “I think it’s quite specialised,” she concedes. “The latest development we see in food and home cooking is that it should not take that much time and we don’t want to putthat much effort into it. Maybe if we have a great development where you can just start talking to your printer, like when you get out of bed, ‘Please prepare breakfast for me!’ We’ll see, but I don’t really believe in it yet.”
Where 3D printing seems to thrive, Hague notes, is in customisation and lightweight design. “You can make super-complex geometries that you just can’t do any other way,” he says. One company taking advantage of the geometric freedom of the technology this is Czinger, the Los Angeles-based car manufacturer. Right now, Czinger only offers one model, the 21C, but it is a head-turner: a hypercar with a top speed of 253mph, a 0-60-time of under 2 seconds, and a price tag of $2m. Parts of cars – especially prototype parts – have been 3D printed for a while, but the 21C goes much further. “It isn’t really a car at all,” wrote Jack Rix, editor of BBC’s Top Gear Magazine in his review of the 21C, “it’s a demonstrator for what’s possible with digital design and 3D printing.”
Czinger is the name and the vision of its founders, dad Kevin Czinger and his son Lukas, 28. Their company has more than 150 employees and they have been recruited from Ferrari and F1 teams but also Apple and SpaceX.
“We both love driving, we both wanted to make a car that would take our breath away,” explains Lukas Czinger on a 7am (for him) video call. “And certainly having that car on the track, it feels like nothing I’ve ever driven, nothing my dad’s ever driven, the downforce, the seating position, the pure power. It’s everything we dreamed of. It’s wild in the best of ways. It’s like being in the cockpit of a fighter jet, but instead of being in the air, you’re somehow still planted to the ground. You don’t fully understand physics any more.”
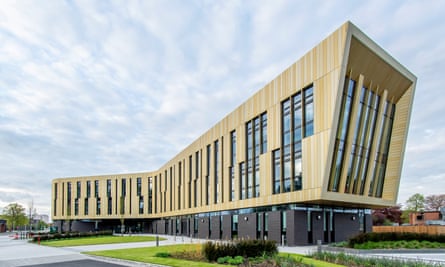
You might legitimately wonder how much relevance a $2m hypercar has to anything in the real world. But Czinger makes parts for at least eight more mainstream automotive brands – the only one they are allowed to name at the moment is Aston Martin. 3D-printed parts can be lighter, more aerodynamic and potentially stronger, Lukas Czinger argues, and all of these developments have a potential environmental benefit, as cars become more fuel efficient. “In the next five years, you’re going to start seeing it on everyday cars,” he predicts. “And in the next 10 years, you’re going to basically have seen it replace most of casting and extruding and stamping. So, yeah, I fully believe it is the future.”
I ask Top Gear’s Rix if he buys Czinger’s claim that the 21C is a “historically significant vehicle” that will fundamentally change the car industry. “Every car manufacturer is continually looking to improve packaging, reduce weight, boost fuel efficiency, but also find ways to build their cars to a higher quality and for less,” Rix replies. “Czinger claims to have solved all these problems in one fell swoop.” As for how influential this technology will be: “It is only a matter of time before all new cars have some 3D-printed parts.”
We’ve been here before, of course: 3D printing will save the world! So why believe it now? There is growing evidence that the hype, this time round, might not be overstated. Not all of these developments will touch our lives immediately. Nasa and all space-exploration companies already use additive processes to make parts for their rockets. But they are also investigating the challenges that will arise once they land on the Moon or Mars . They will not be able to carry all the resources with them, so they have to find methods for construction and providing food: perhaps using the directed energy from the sun and the materials they will find on the ground. Nasa funds one project that is looking into recycling the urine, faeces and breath of astronauts on long journeys to make food and plastics for 3D printing.
But, if it hasn’t already, additive manufacturing will soon touch – and even, maybe, extend – all of our lives. The American company Stryker uses 3D printing to produce complex orthopaedic implants that wouldn’t otherwise be possible. In the US last year, a woman’s ear was reconstructed with an implant of 3D-printed living tissue. A human lung scaffold was presented at a conference in San Diego last summer, possibly the most complicated object ever created using additive manufacturing.
The University of Nottingham’s Richard Hague is currently working with GSK and AstraZeneca on the 3D printing of “biopills” – multiple medicines in a single pill that are bespoke to each patient, which will dramatically simplify what you need to take and when, especially for elderly people. “Compliance is a massive issue: you’ve got all these drugs, people just don’t take them,” says Hague. “These are huge potential benefits that people can understand.”
This is where the promise of 3D printing becomes irresistible – where the technology clearly makes life simpler or better, with no extra expense for the consumer. In Accrington, Building for Humanity wants to put people on the housing ladder who otherwise would never be able to afford it. One of the houses has been reserved for Mark Harrison, 44, a veteran from the town who received a medical discharge from the Army in 2001 after two tours in Bosnia, and was later diagnosed with PTSD.
Harrison estimates he has lived in 20 houses in the last 20 years, but hopes Charter Street will provide stability for him and his three children. He is also being trained up by HTL to use the printing machinery – he could have a new job as well as having a hand in building his new home.
“All these years I’ve been going to therapy and I’m trying my hardest to kick on and get better,” says Harrison. “The house would be the icing on the cake. It’ll give me somewhere to put down some roots: something for my kids’ future and for me to stay in the same place for more than two minutes. It’s been difficult, but yeah, it’s an incredible opportunity. It just seems like everything has finally fallen into place.”